Hello there!
As some of you know, some time ago I've started a conversion for the Trumpeter's 1:144 Astute. I thought I'll make that boat and complete my 1:144 RC collection as I already had all the other 3 Trumpeter 1:144 models converted to RC (Soryu, Kilo and the Seawolf). Sadly, at some point the build was held cause of overwhelming amount of work, so now - as I'll have some spare time, I plan to finish this model. I thought It might be a nice idea to show people a wider audience how I'm dealing with that little rascal.
So first let's get up to date what's has been already finished:
The box content is very modest. We get the hull split into two parts (upper and lower) and two frames of elements, where one of these frames is only the boat stand. Very, very modest content even for a modern sub. The hull lacks many details and looks a lot more poorer and simpler than for example the Soryu model – which has lots of hull details – including the square plated anti sonar square coating.
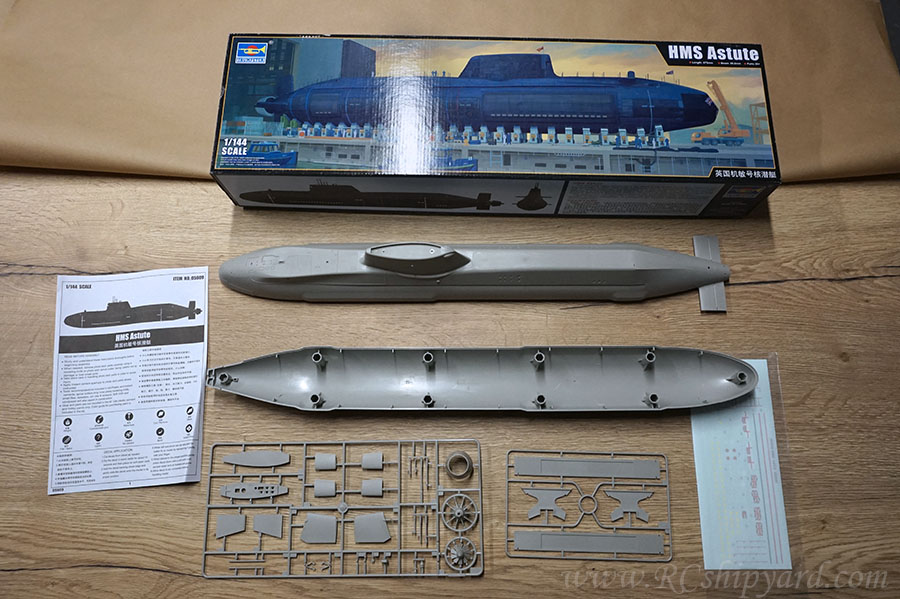
The hull itself is quite thick - which is good, but requires some work, if we want to fit a 50mm (about 1.96inch) WTC inside. So first I had remove the 3 pairs of the middle pillars and the single one in the stern.
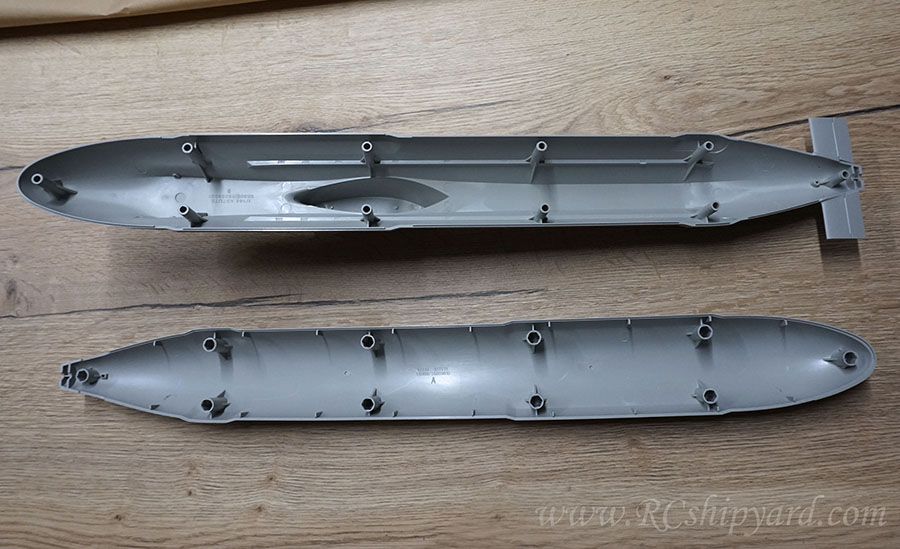
Removing the pillars was an easy job in general. I’ve used my trusty Proxxon mini cutter with a disc bit at first, then a bit with a pink sanding stone.
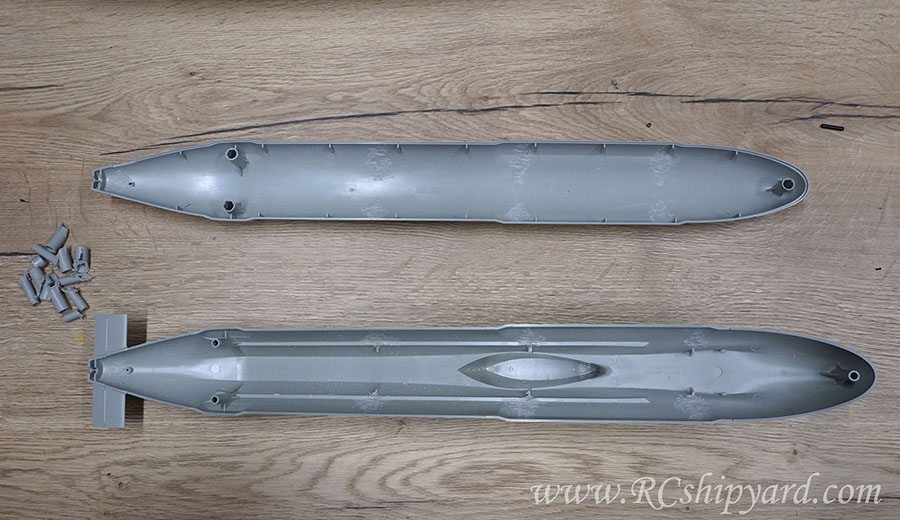
And as in everything - if you'll feel a little to confident when you're doing something - a mistake will likely to happen – I did cut through the hull at one point. Not a big deal as it’s an easy thing to repair with Tamiya putty, but I should have been more careful when cutting out one of the pillars:
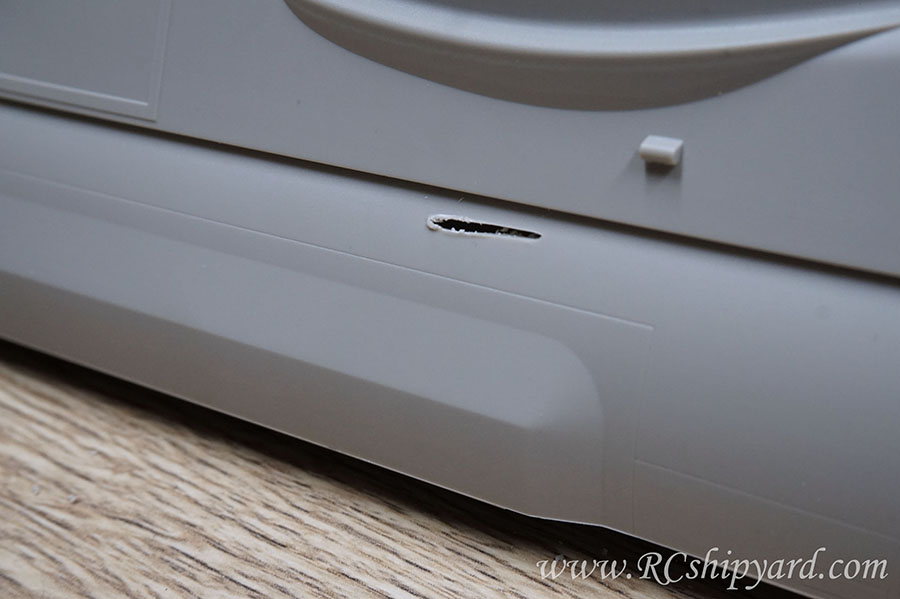
With the pillars gone the time came for the stern diving planes, which sadly are a solid part of the hull in all the new Trumpeter 1:144 models, so they’ll have to be removed:
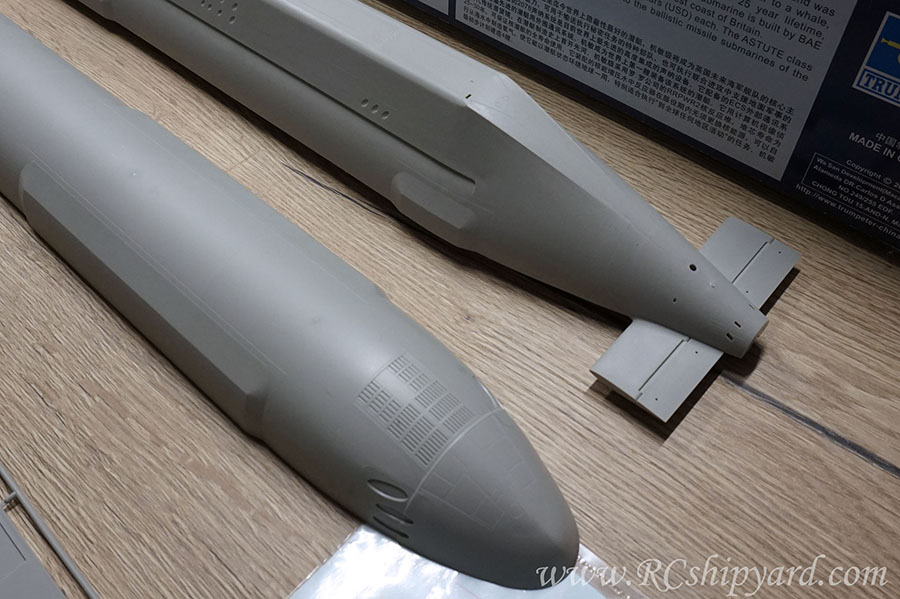
After successfully removing one of the stern diving planes, I thought that it might be a good idea to explain in detail how I did it, instead of simply showing the result. All the used tools on one picture:
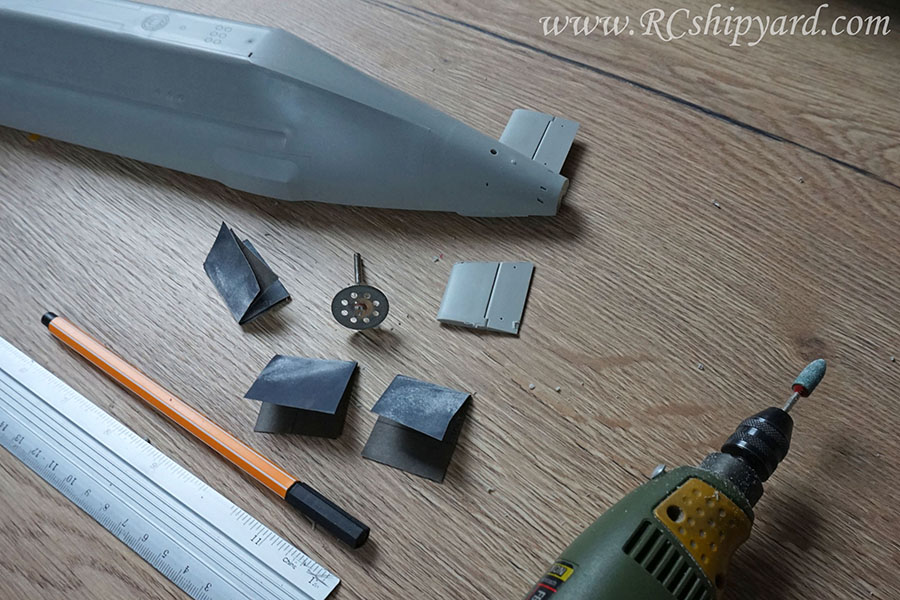
So at first, I like to mark myself the line of cut with some margin of space from the main hull. One reason for this is because the cutting discs are fixed to the cutting bit with a screw and I don’t want that screw to scratch the hulls surface. I usually use a simple ruler for that:
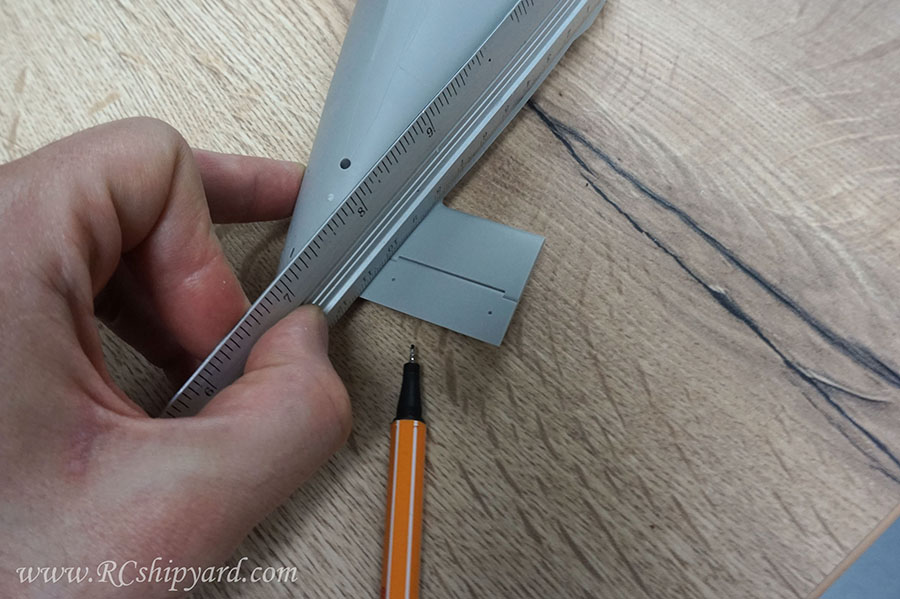
I end up with an straight line which differs in thickness, but that really doesn’t matter, as the cutting disc itself is thicker than the line.
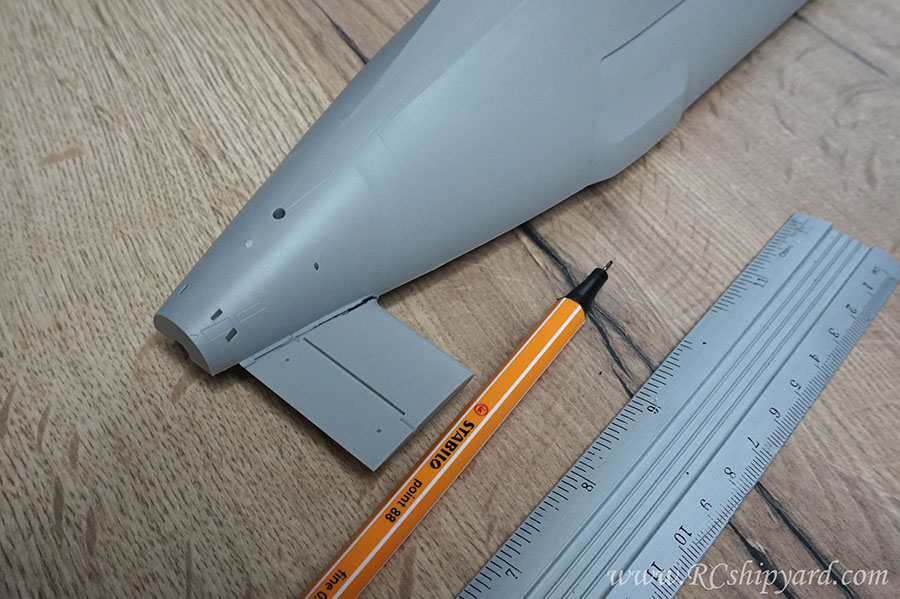
The cut looks rough, but it has to look like this as the plastic melts from a high speed Proxxon cut – even at it’s lowest speed setting of 4000 RPM. However because of the margin of space between the hull and the line of cut, the melted plastic has lot’s space to cool down without damaging the hull (that's the second reason for drawing that line a bit further from the hull):
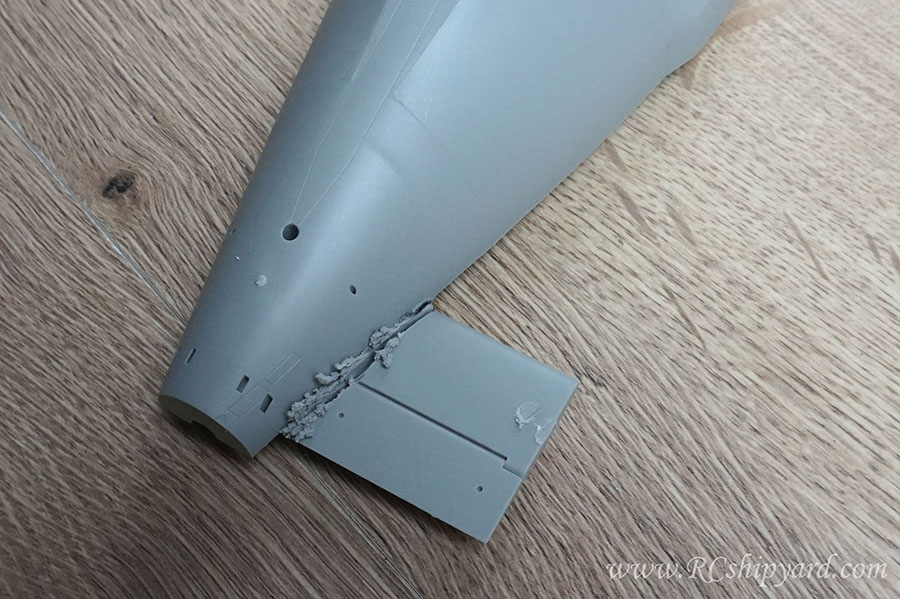
After removing the melted plastic with bare hands, as it simply cracks off and of course after some sanding with 3 grades of sanding paper – I end up with a very nice surface finish.
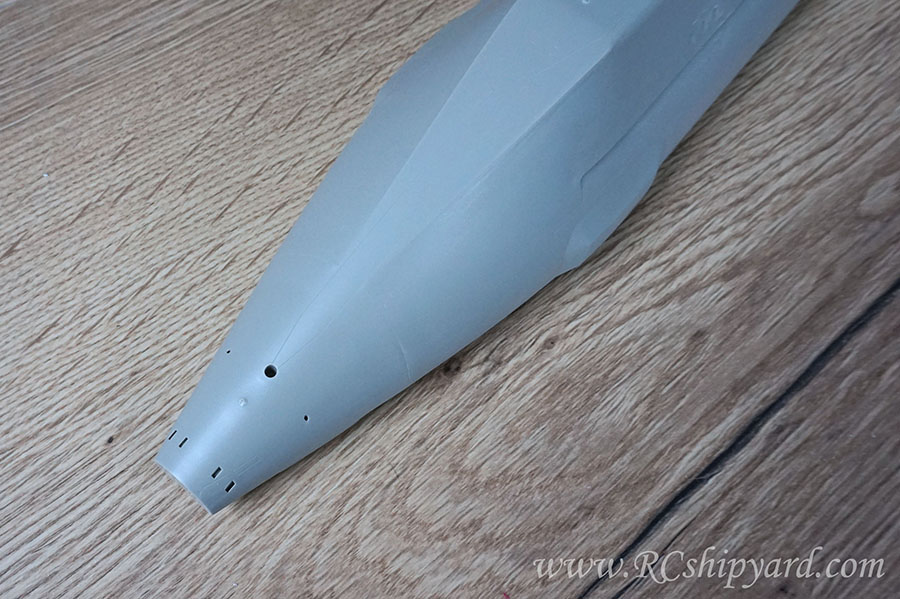
Hard to believe there were any diving planes there in the first place, right?
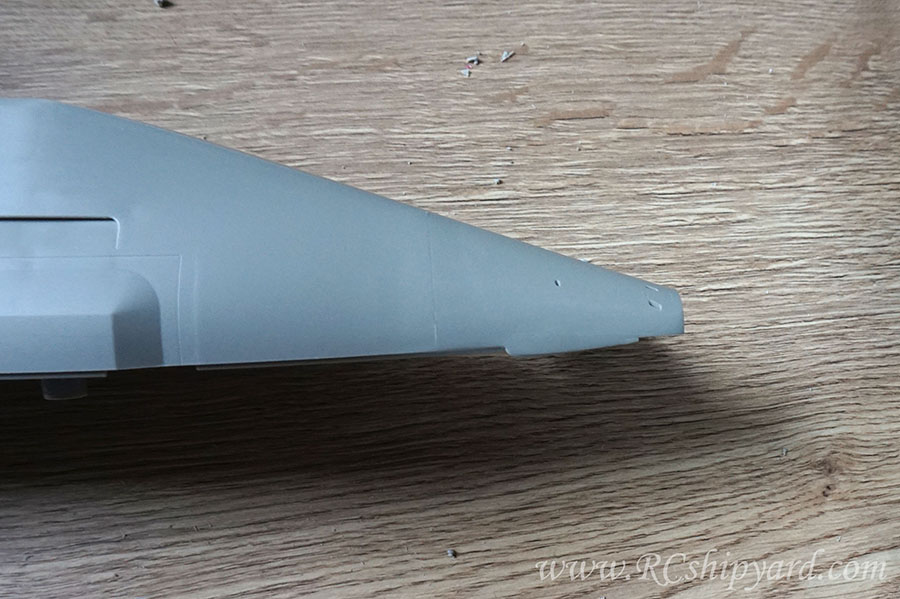
More soon!
As some of you know, some time ago I've started a conversion for the Trumpeter's 1:144 Astute. I thought I'll make that boat and complete my 1:144 RC collection as I already had all the other 3 Trumpeter 1:144 models converted to RC (Soryu, Kilo and the Seawolf). Sadly, at some point the build was held cause of overwhelming amount of work, so now - as I'll have some spare time, I plan to finish this model. I thought It might be a nice idea to show people a wider audience how I'm dealing with that little rascal.
So first let's get up to date what's has been already finished:
The box content is very modest. We get the hull split into two parts (upper and lower) and two frames of elements, where one of these frames is only the boat stand. Very, very modest content even for a modern sub. The hull lacks many details and looks a lot more poorer and simpler than for example the Soryu model – which has lots of hull details – including the square plated anti sonar square coating.
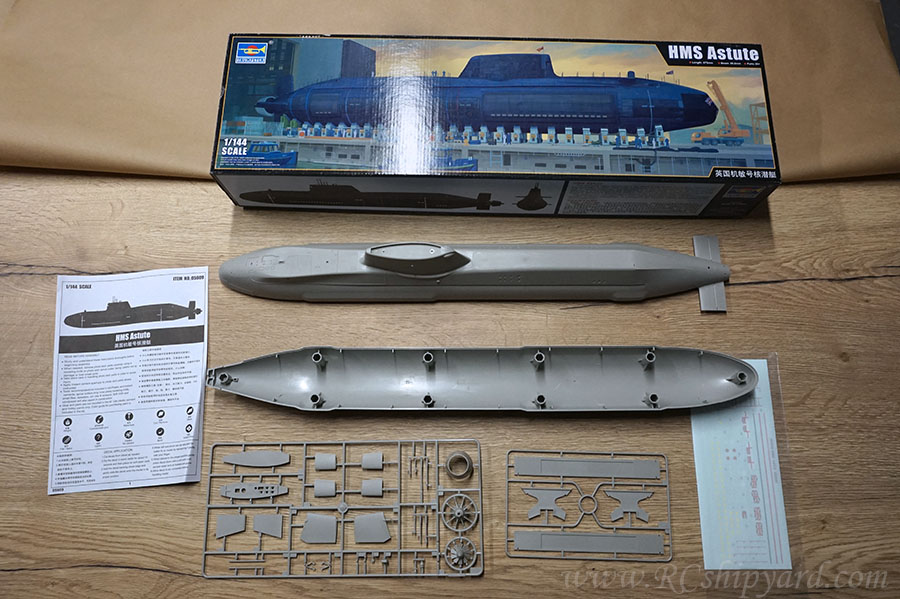
The hull itself is quite thick - which is good, but requires some work, if we want to fit a 50mm (about 1.96inch) WTC inside. So first I had remove the 3 pairs of the middle pillars and the single one in the stern.
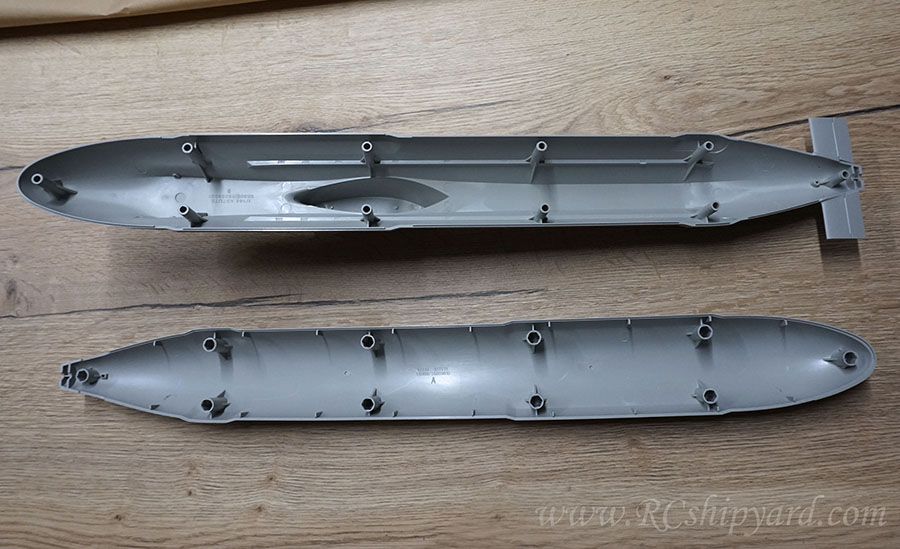
Removing the pillars was an easy job in general. I’ve used my trusty Proxxon mini cutter with a disc bit at first, then a bit with a pink sanding stone.
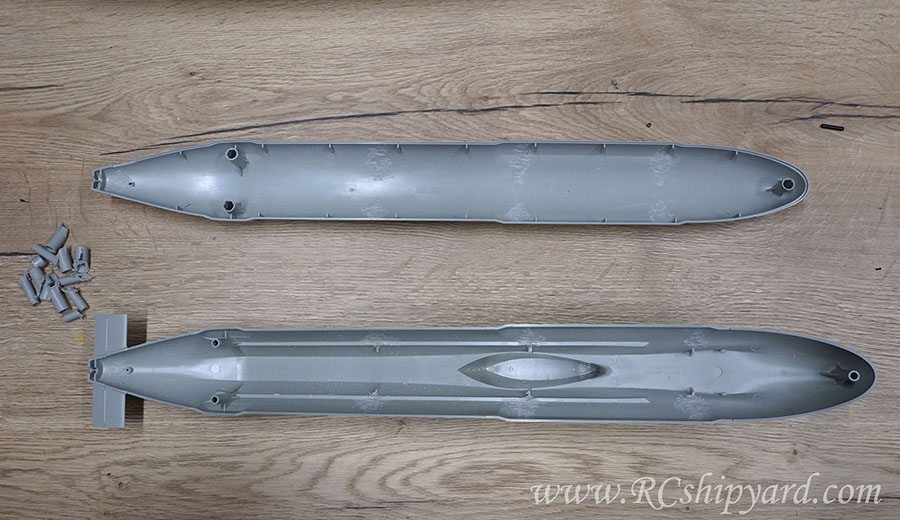
And as in everything - if you'll feel a little to confident when you're doing something - a mistake will likely to happen – I did cut through the hull at one point. Not a big deal as it’s an easy thing to repair with Tamiya putty, but I should have been more careful when cutting out one of the pillars:
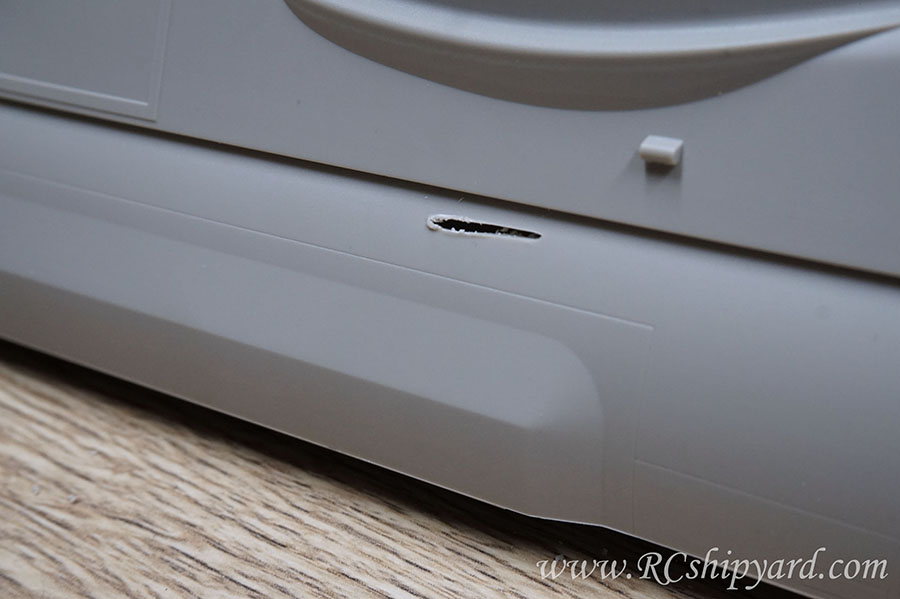
With the pillars gone the time came for the stern diving planes, which sadly are a solid part of the hull in all the new Trumpeter 1:144 models, so they’ll have to be removed:
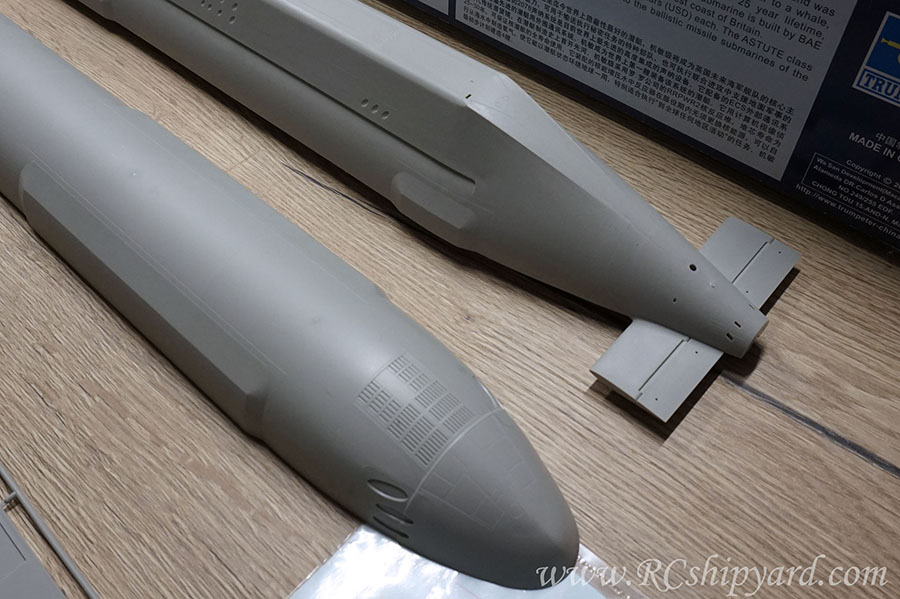
After successfully removing one of the stern diving planes, I thought that it might be a good idea to explain in detail how I did it, instead of simply showing the result. All the used tools on one picture:
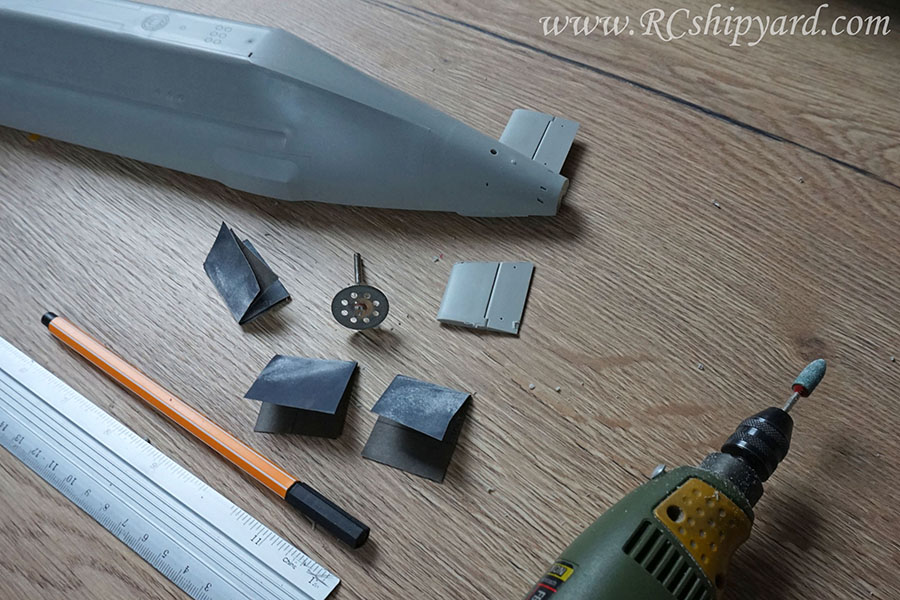
So at first, I like to mark myself the line of cut with some margin of space from the main hull. One reason for this is because the cutting discs are fixed to the cutting bit with a screw and I don’t want that screw to scratch the hulls surface. I usually use a simple ruler for that:
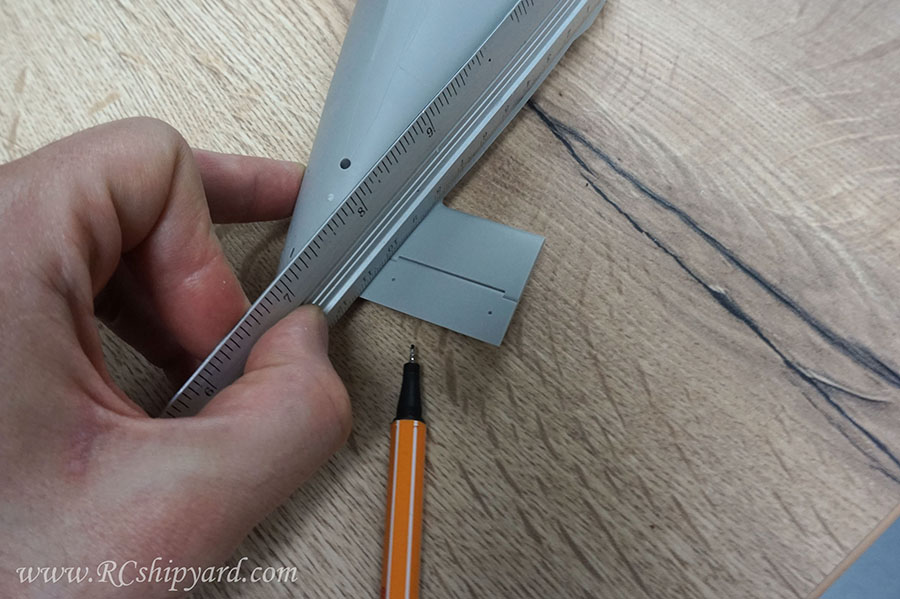
I end up with an straight line which differs in thickness, but that really doesn’t matter, as the cutting disc itself is thicker than the line.
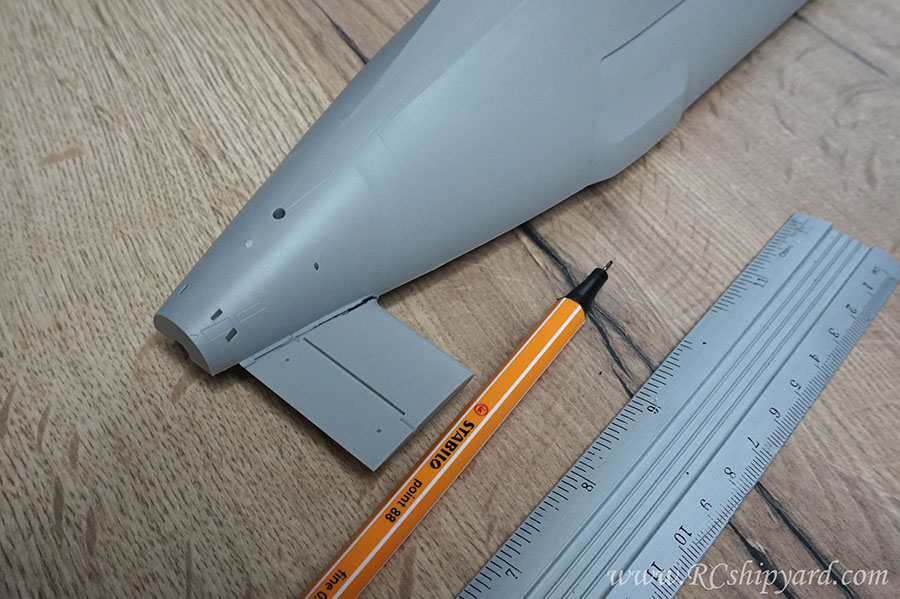
The cut looks rough, but it has to look like this as the plastic melts from a high speed Proxxon cut – even at it’s lowest speed setting of 4000 RPM. However because of the margin of space between the hull and the line of cut, the melted plastic has lot’s space to cool down without damaging the hull (that's the second reason for drawing that line a bit further from the hull):
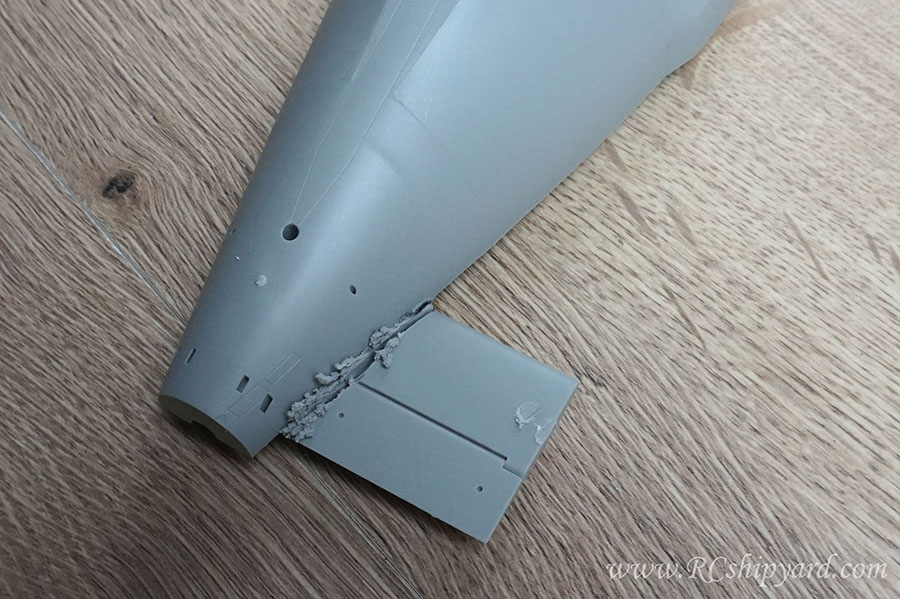
After removing the melted plastic with bare hands, as it simply cracks off and of course after some sanding with 3 grades of sanding paper – I end up with a very nice surface finish.
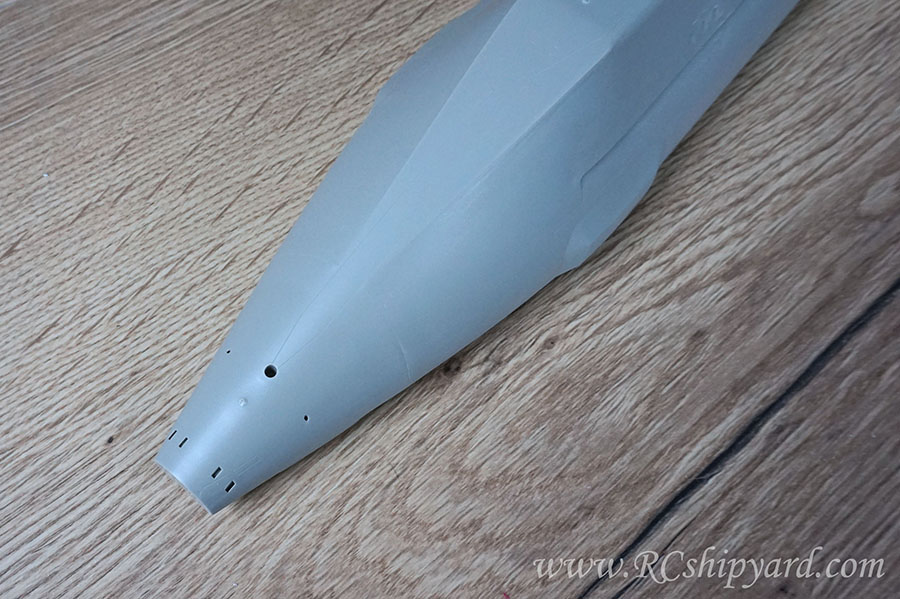
Hard to believe there were any diving planes there in the first place, right?
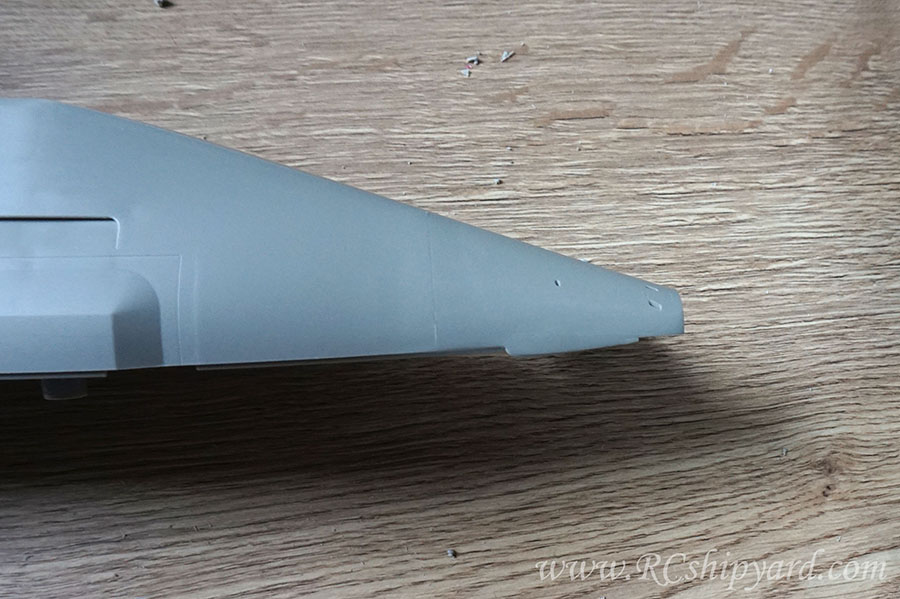
More soon!
Comment