I thought I would start this thread to get some input on what some good budget lathes and drill presses might be for WTC end cap construction. Subculture Andy, could probably chime in here, as he has done this kind of thing, numerous times.. With a few units like the ones I have shown, perhaps for the cost of one commercial WTC, you could buy these machines, and make your own WTC. Then you could make additional WTC units, for much less in the future. If you're only interested in having one WTC and one sub, this route probably wouldn't be worthwhile for you..
This would also be good if you can't locate a commercial WTC unit that fits the particular model you're interested in building, and fits into the layout you'd like to have in your sub. Maybe currently available commercial units, don't provide you enough room for torpedo launchers, etc.. Or maybe you want a 2.75" OD WTC. Most commercial units are either 2.5" or 3.0".
Another good discussion would be how to make your own motor bulkhead endcap. So that you can attach the drive motor or motors, of YOUR choice, to the endcap, with a propshaft seal or seals installed in the bulkhead cap.
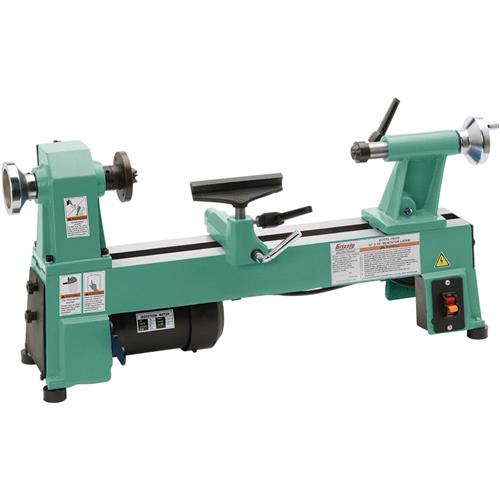
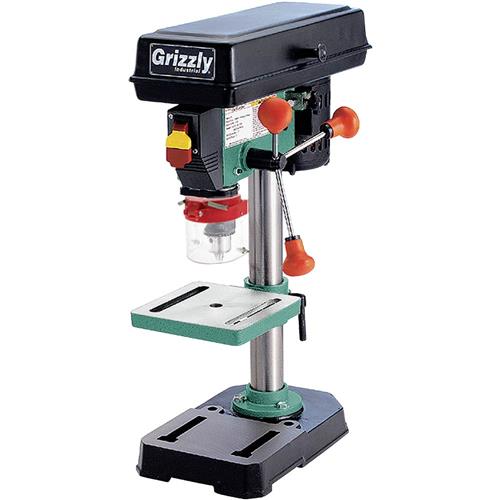
This would also be good if you can't locate a commercial WTC unit that fits the particular model you're interested in building, and fits into the layout you'd like to have in your sub. Maybe currently available commercial units, don't provide you enough room for torpedo launchers, etc.. Or maybe you want a 2.75" OD WTC. Most commercial units are either 2.5" or 3.0".
Another good discussion would be how to make your own motor bulkhead endcap. So that you can attach the drive motor or motors, of YOUR choice, to the endcap, with a propshaft seal or seals installed in the bulkhead cap.
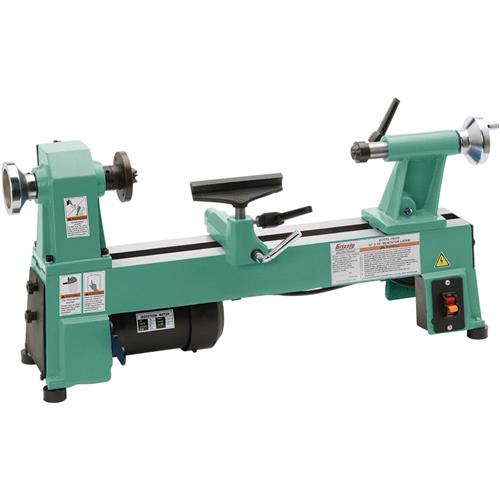
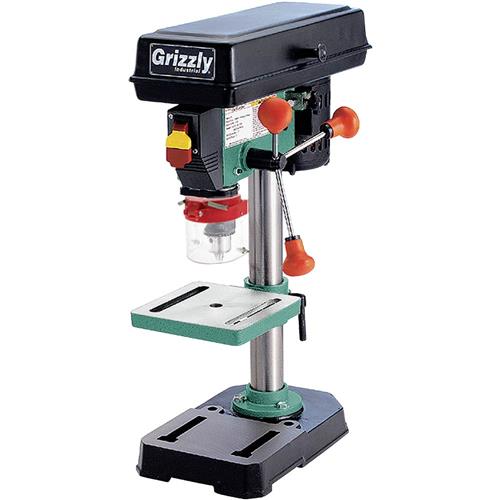
Comment